(AMÓS ZEEBERG. THE NEW YORK TIMES)
En junio, el Ministerio de Cultura italiano anunció la excavación de una nueva sala, aún no abierta al público, en las ruinas de Pompeya. Unas semanas después, un grupo de arqueólogos se reunió para admirarla: paredes cubiertas de pintura azul brillante (un pigmento caro reservado para salas especiales) y frescos detallados de imágenes agrícolas notablemente bien conservadas después de casi 2000 años.
Admir Masic, químico del MIT, se sintió más cautivado por lo que, para un invitado no especializado, parecía un montón de tierra arenosa sin nada destacable en el borde de la habitación. El material, de color canela claro y granulado, había sido un componente fundamental del Imperio romano, dijo: el precursor del hormigón, un pilar de la infraestructura romana, incluidos los acueductos que llevaban agua dulce a ciudades como Pompeya.
“Consiguieron llevar agua a la ciudad y, con ella, la higiene”, afirmó el Dr. Masic. “Ese avance tecnológico les permitió, en primer lugar, construir Roma tal como es, pero también reproducirla en cualquier lugar al que fueran”. Extendió los brazos como si estuviera describiendo todo el mundo romano.
El hormigón moderno, basado en un material conocido como cemento Portland, se desarrolló en Inglaterra en el siglo XIX y es, con diferencia, el material de construcción más popular del mundo. Es barato, resistente y estandarizado, lo que proporciona a los ingenieros de todo el mundo un material sencillo para construir apartamentos, presas, rascacielos y mucho más. Pero es mucho menos resistente que el hormigón utilizado en la época romana; con el paso de las décadas, desarrolla grietas que, al dejar entrar el agua, pueden acabar destruyendo el material.
Además, la fabricación de hormigón es uno de los principales impulsores del cambio climático, ya que produce el 8 por ciento de las emisiones de dióxido de carbono en todo el mundo. Al aprender los secretos del hormigón romano, investigadores como el Dr. Masic están tratando de idear opciones modernas más ecológicas y duraderas.
“Los hormigones marinos romanos han sobrevivido en uno de los entornos más agresivos de la Tierra sin necesidad de mantenimiento alguno”, afirmó Marie Jackson, geóloga de la Universidad de Utah.
Una sustancia autocurativa

El hormigón romano obtiene gran parte de su resistencia de una mezcla de hidratos de aluminato de calcio y silicato, conocidos como CASH, con diferentes fórmulas químicas. Pero no está claro exactamente cómo producían los romanos ese material.
La creencia tradicional es que los romanos calentaban piedra caliza, compuesta principalmente de carbonato de calcio, para producir un material peligrosamente reactivo llamado cal viva u óxido de calcio. Luego añadían agua, formando hidróxido de calcio o cal apagada. Finalmente, combinaban esto con un material voluminoso, a menudo ceniza volcánica, que aportaba el aluminio y el silicio necesarios para el hormigón (la A y la S de CASH).
Masic ve un problema con esta explicación. Muchos ejemplos de hormigón romano, señaló, contienen trozos blancos visibles, o clastos. “Estos se ven en todas partes: en Roma, en África, en Israel”, dijo.
Generalmente se piensa que los trozos son productos involuntarios de un trabajo deficiente, pero el Dr. Masic sostiene que los ingenieros romanos eran demasiado inteligentes como para fabricar constantemente hormigón plagado de errores. “La gente decía que los clastos de cal son una mala mezcla de cal apagada”, dijo. “Nuestra hipótesis es que no es parte de un mal procesamiento; es parte de la tecnología”.
Según la investigación del Dr. Masic, estos clastos de cal eran en realidad depósitos de calcio que ayudaban a rellenar las grietas, lo que hacía que el hormigón se autocurara. A medida que se formaban las grietas, el agua se filtraba y disolvía el calcio de la cal, que luego formaba carbonato de calcio sólido, creando básicamente roca nueva que rellenaba la grieta.



Un fresco que muestra la pintura azul brillante de la sala recién inaugurada; una imagen electrónica de barrido de una antigua muestra de hormigón romano con clasto de cal, resaltada en rojo; el Dr. Masic inspeccionando los frescos de las paredes de hormigón en Pompeya.Crédito…Amos Zeeberg, cortesía del MIC — Parque Arqueológico de Pompeya; James Weaver; Amos Zeeberg, cortesía del MIC — Parque Arqueológico de Pompeya
El Dr. Masic sostiene que los clastos de cal no procedían de cal apagada, sino de cal viva que los romanos añadían directamente, en un proceso llamado mezcla en caliente. Como la cal viva es tan reactiva, genera calor cuando se combina con ceniza volcánica, calentando el material a más de 170 grados Fahrenheit, lo que hace que el hormigón se endurezca mucho más rápido. La técnica también generó algunos puntos calientes de casi 400 grados, lo que provocó que parte de la cal viva quedara en pequeños trozos intactos: los clastos que se ven en el hormigón romano actual y que proporcionan sus propiedades autocurativas, dijo el Dr. Masic.
Pero es difícil demostrar que los romanos dejaron intencionalmente trozos de cal viva en el hormigón, porque los trozos cambiaron químicamente a lo largo de los siglos. Al examinar los clastos con microscopios especiales, dijo el Dr. Masic, él y sus colegas han demostrado que los clastos en realidad comenzaron siendo cal viva.
El Dr. Masic ha derivado su investigación a una empresa llamada DMAT, cuyo objetivo es integrar los principios de la química del hormigón romano en la versión moderna. La empresa vende un aditivo que, según afirma, sella las grietas del hormigón, lo que, en teoría, reduciría la dependencia del cemento Portland, con su gran huella de carbono. “Generamos más resistencia, generamos más agente aglutinante”, dijo Paolo Sabatini, director ejecutivo de la empresa. “Cuando hacemos eso, utilizamos menos hormigón”.

Reacciones volcánicas
No todos los investigadores están convencidos de que la mezcla en caliente fuera la clave del hormigón autorreparador de los romanos. La Dra. Jackson sostiene, en cambio, que el secreto residía en los materiales voluminosos que se mezclaban con cal, a menudo un tipo de ceniza volcánica llamada puzolana. La puzolana, que recibe su nombre de la ciudad costera de Pozzuoli, en Italia, donde se excavó gran parte de ella, activaba reacciones químicas especiales que conferían al hormigón romano su durabilidad inigualable, según su investigación.
La reacción inicial de la cal y la puzolana generó los compuestos CASH que actuaban como pegamento en el hormigón de la antigua Roma. Y los materiales continuaron reaccionando, formando minerales raros como la esträtlingita durante muchos años después de que se fabricara el hormigón, descubrió la Dra. Jackson. Los cristales de esträtlingita, con forma de escamas y agujas, ayudaron a unir trozos ásperos de material en el hormigón y bloquearon el crecimiento de grietas. “Este endurecimiento del hormigón parece ser fundamental para la resiliencia a largo plazo”, dijo, y “contribuye a reforzar la cohesión a lo largo de los siglos”.
La Dra. Jackson y sus colaboradores han puesto a prueba sus hipótesis sobre el hormigón antiguo creando análogos modernos del mismo. En un experimento, los investigadores construyeron arcos de hormigón, los sumergieron en agua de mar durante 50 días y luego empujaron la parte superior de los arcos con una presión cada vez mayor hasta que el hormigón empezó a doblarse y a agrietarse. Luego, los arcos se sumergieron durante casi un año y se volvieron a probar. Los investigadores descubrieron que los compuestos CASH habían rellenado las pequeñas grietas y que los arcos podían soportar entre dos y tres veces más fuerza que antes, dependiendo de la prueba en particular. Luego, el equipo sumergió los arcos una vez más. A finales de este mes, planean volver a probarlos después de casi tres años en agua de mar.
“La forma en que los romanos eligieron los materiales en realidad impidió la propagación de las fracturas”, dijo el Dr. Jackson. “Ellos eran los maestros”.


La Dra. Jackson y sus colaboradores creen haber determinado exactamente cuándo los romanos alcanzaron esta maestría: en el siglo I a. C., durante la última etapa de la República. El Teatro de Marcello y los Mercados de Trajano —dos sitios de Roma que la Dra. Jackson ha estudiado— “registran este avance”, afirmó.
Warda Ashraf, ingeniera civil de la Universidad de Texas en Arlington, ha desarrollado un hormigón de inspiración romana para utilizar bajo el agua con el fin de construir puentes, rompeolas y arrecifes artificiales más duraderos y al mismo tiempo ofrecer tanta resistencia como el hormigón moderno normal.
La innovación clave fue utilizar arcilla cargada con caolinita, un material barato y ampliamente disponible, para reemplazar la ceniza volcánica en la receta antigua. “Tomamos eso y usamos exactamente las mismas proporciones que usaban los ingenieros romanos antiguos”, dijo.
Para que la arcilla fuera químicamente activa, la calentaron a unos 1.300 grados Fahrenheit. En cambio, el cemento Portland común debe cocerse en un horno a unos 2.600 grados Fahrenheit. “Es un gran ahorro” de energía, dijo, que lleva a “una reducción del 70 por ciento de la huella de carbono”.
Los investigadores probaron su creación en aguas poco profundas del Golfo de México. Fabricaron docenas de objetos de hormigón (cilindros, cubos, discos) y los colocaron en jaulas. Luego contrataron a buzos para que instalaran las jaulas en el fondo marino a unos cuatro metros de profundidad. Un año después, la resistencia del hormigón había aumentado sustancialmente, por lo que la Dra. Ashraf y sus colegas salieron a celebrar. “Fuimos a un restaurante italiano”, dijo.
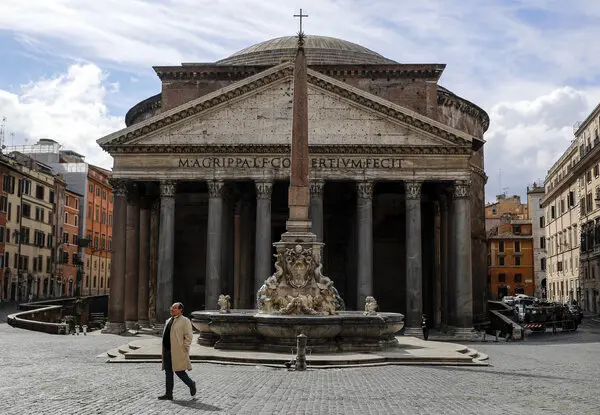
El Panteón de Roma cuenta desde hace 2.000 años con la cúpula de hormigón sin soporte más grande del mundo.Crédito…Riccardo Antimiani/EPA, vía Shutterstock